Cutting Edge Tech
Our fiber photonics innovations open up a whole world of capabilities for optical fiber-based technology and potential customer applications. HighRI’s diverse team of dedicated research scientists and highly-skilled engineers have the knowledge and creativity to drive the adoption of and use of fiber photonics.
The main advantage of the fiber photonics technology is that the diffractive element is always connected to the light source – optical fiber. This makes the use of such devices extremely easy. Simply connect the fiber to a fiber coupled laser, and the desired light profile comes out of the other end. No free-space optics is required. There is no need to worry about the input beam shape because the fiber mode profile always remains the same. This makes fiber photonics devices very stable, compact and reliable. Advantages of having diffractive optics on fiber:
- Easy to use – no assembly or alignment
- Compact – the diffractive element is approximately the size of the fiber core
- Ultimate optical performance through free-form design
- Optical stability
- Reproducible fabrication
- High refractive index lens possible for immersion applications
Use Cases And Applications
Our variety of fibers have a depth of uses, while each one varies, some include:
- Fiber to Chip Coupling
- Compact Collimation
- Data Communication
- Material Processing
- Optical Trapping
- Super-resolution Imaging
- Telecommunication
Vortex Fibers
Vortex fibers produce an optical vortex without the optical alignment or bulky free-space optics. This reduces time, cost, and space. Making the end application more efficient and facilitating ease of design and reproducibility.
The resultant optical vortex beam has two main features, angular momentum and donut shape. These features then carry over to two main types of applications. Angular momentum is used in telecommunications to transmit information or in optical trapping to rotate microparticles. Zero intensity at the axis is used in STED microscopy to achieve subdiffraction imaging.
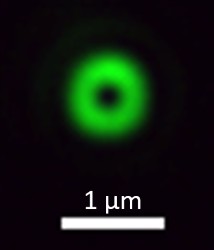
Advantages:
- No optical alignment is necessary
- Stability and reproducibility
- Ease of integration
- Small size
Applications:
- STED microscopy
- Telecommunication
- Optical trapping
Flat-Top BeamShaper
A flat top beam shaper creates a far field profile with a uniform intensity in its center. Conventional diffractive beam shaper requires accurate alignment and beam control. Input beam diameter and profile have to be exactly right. Unlike the free-space diffractive element, the beam shaper fabricated on the facet of a fiber does not require any alignment. For such beam shaper, the input beam is a fiber mode that does not change in time, providing a reproducibility and long term stability.
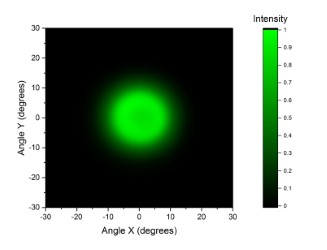
Advantages:
- No alignment required
- Long term stability
- Highly reproducible
- Compact size
- Controlled beam divergence
Applications:
- Illumination
- Holography
- Microscopy
- Displays
- Material processing
Compact Fiber Collimators
Fiber collimator reduces the divergence angle of the light output from an optical fiber. Fiber collimators are used to match the beam divergence from a fiber with the optical setup and/or coupling light into the fiber from free space. Unlike the conventional approach to use GRIN lenses, we use a 3D diffractive lens patterned on the fiber edge for simplified operation.

Advantages:
- No alignment required
- Monolithic design
- Highly reproducible
- Extremely compact size
Applications:
- Fiber coupling
- Divergence angle control
- Collimation
Lensed Fibers
Lensed fiber is an optical fiber with a tip shaped like a lens. Lensed fibers are used in integrated optics, optical trapping, and fiber sensors. Lens fiber creates a tight focal spot at a distance away from the fiber edge. This tight focal spot can couple light into an optical chip, collect light from a laser diode, or even trap a microparticle.
Conventional lensed fibers are made using polishing, laser cutting, or plasma arc. All these techniques restrict the shape and material of the lens, which limits the performance and potential applications. Using our fiber nanoimprint technology, we were able to remove these constraints. Our lensed fibers have free-form lenses and can be made out of high refractive index materials for immersion applications.
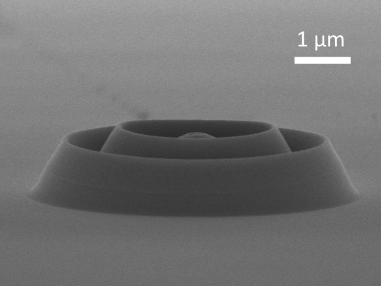
Advantages:
- Near diffraction-limited focal spot
- Elliptical or circular focal spot options
- High refractive index
- Immersion compatible
- Highly reproducible
Applications:
- Immersion applications
- Laser-to-fiber coupling
- Integrated optics
- Optical trapping
- Biosensors
- Material processing
Custom Fiber Solutions
Custom fiber solutions are available. If you can envision an optical application we don’t have listed or need help prototyping, we can help. At HighRI, we have the capability of fast-tracking ideas into products. We design, simulate, fabricate, characterize, and produce nanoscale optical and photonic components. HighRI supports the entire suite of production from planning to fabrication.
Advantages:
- Optimized optical performance through free-form design
- High refractive index materials for fiber imprinting